Gia công cắt gọt là phương pháp sử dụng máy gia công để tạo ra sự di chuyển mà ở đó dụng cụ cắt và phôi sẽ giao thoa với nhau, dẫn tới việc những phần không cần thiết của phôi sẽ bị gọt đi. Được ra đời từ cuối thế kỉ 18, đến đầu thế kỉ 20 thì máy gia công bắt đầu phát triển vũ bão đến ngày nay, với sự ra đời của máy NC (Numerical Control), sau đó là máy CNC (Computer Numerical Control) và hiện tại là ứng dụng các sensor và AI vào máy CNC để giúp máy thông minh hơn, nâng cao năng suất.
Ta đều biết máy móc công nghiệp được cấu thành bởi rất nhiều chi tiết lắp ghép lại với nhau. Ví dụ như số chi tiết trong một chiếc xe ôtô có thể lên đến khoảng 30 nghìn chi tiết, hoặc một chiếc máy bay có thể cần đến 3 triệu chi tiết. Hầu hết những chi tiết này được chế tạo từ kim loại hoặc phi kim loại như nhựa hoặc cao su, v…v… Và chúng đều có một điểm chung là được gia công bằng một phương pháp nào đó từ vật liệu ban đầu, vật liệu ban đầu này trong sản xuất được gọi là phôi. Tóm lại, gia công có thể hiểu đơn giản là việc đưa năng lượng và thông tin ở đầu input (đầu vào), thông qua đó chuyển hóa phôi trở thành sản phẩm ở đầu output (đầu ra).
Hình 1. Quá trình gia công
Tuy nhiên, để thực hiện việc gia công một cách hiệu quả thì kích thước (寸法), độ chính xác về hình dáng (形状精度), yêu cầu về độ nhám bề mặt của sản phẩm cuối cùng (仕上げ面粗さ), tính chất bề mặt (表面特性), sức bền (強度), độ cứng (硬度) của vật liệu đều phải được suy xét đến. Tổng quan thì chúng ta có những phương pháp gia công chủ yếu sau đây.
- Đúc (鋳造)
- Biến dạng dẻo (塑性加工)
- Ép phun tạo hình (射出成形)
- Gia công mối nối (接合加工)
- Gia công cắt gọt (切削加工)
- Gia công mài (研削加工・砥粒加工)
- Gia công đặc biệt (特殊加工)
- Xử lý bề mặt (表面処理)
Ngoài ra, những năm gần đây đã bắt đầu phổ biến phương pháp tạo hình phân lớp (積層造形) hoặc có tên khác là sản xuất bồi đắp (付加製造, Additive Manufacturing, AM), hay thường được biết đến với tên gọi mà ai cũng biết là in 3D. Đây là phương pháp kết dính các tầng vật liệu mỏng để tạo thành hình dáng 3D tùy ý. Ví dụ như Hình 2.
Hình 2. Một ví dụ về in 3D
Theo flowchart ở Hình 3 thì các sản phẩm đúc và dập thường không được sử dụng như sản phẩm cuối cùng mà thường chỉ tạo ra hình dáng cơ bản của phôi, rồi sau đó phôi sẽ được dùng trong gia công cắt gọt để hoàn thiện theo độ chính xác được yêu cầu. Gia công cắt gọt xử lý được hầu hết các loại biên dạng của các chi tiết, tuy nhiên ở công đoạn sau thì đôi lúc vẫn cần đến những phương pháp như tôi thép (gia nhiệt cho thép lên đến 1 nhiệt độ cần thiết rồi làm lạnh nhanh, ví dụ như thợ rèn nhúng kiếm đang nóng đỏ vào nước lạnh để làm bề mặt kiếm cứng hơn), xử lý nhiệt hoặc gia công mài để đạt được độ nhám bề mặt được yêu cầu.
Hình 3. Quy trình gia công một chi tiết thông thường
Gia công cắt gọt được sử dụng phổ biến nhất trong tất cả các loại gia công do cân bằng được 3 yếu tố: Giá thành, tốc độ gia công và độ chính xác. Cụ thể của các đặc điểm được trình bày như Bảng 1.
Bảng 1. Các yếu tố khi gia công và khả năng đáp ứng của gia công cắt gọt
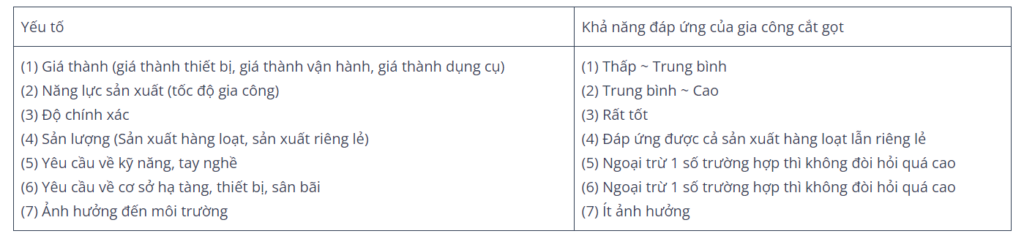
Định nghĩa của gia công cắt gọt sẽ được trình bày kỹ hơn ở những bài sau. Tuy nhiên, để nói 1 cách đơn giản thì gia công cắt gọt là phương pháp sử dụng máy gia công để tạo ra sự di chuyển mà ở đó dụng cụ cắt và phôi sẽ giao thoa với nhau, dẫn tới việc những phần không cần thiết của phôi sẽ bị gọt đi. Được ra đời từ cuối thế kỉ 18, đến đầu thế kỉ 20 thì máy gia công bắt đầu phát triển vũ bão đến ngày nay, với sự ra đời của máy NC (Numerical Control), sau đó là máy CNC (Computer Numerical Control) và hiện tại là ứng dụng các sensor và AI vào máy CNC để giúp máy thông minh hơn, nâng cao năng suất.
Hình 4. Quá trình phát triển và lịch sử của máy gia công
Hình 5. DMU 125 FD duoBLOCK (DMG Mori)
Thân bút, 🖊
Đậu Xanh
#giacông #giacôngcơkhí #CNC
#Pinus
#đặcđiểmvàchỗđứngcủagiacôngcắtgọttrongngànhsảnxuất